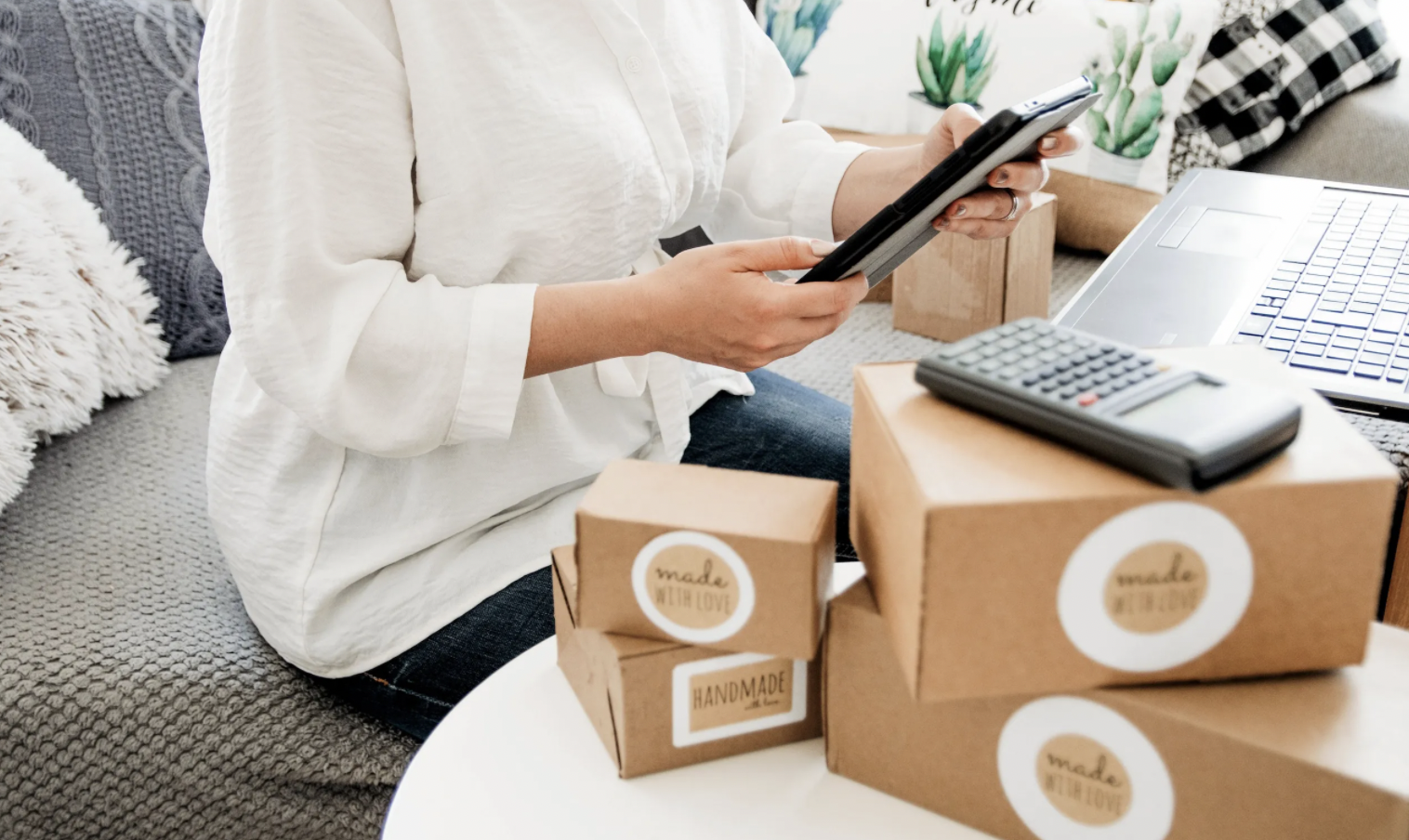
Custom boxes are made to order and can be tailored to your specific needs. They offer a lot of advantages over traditional packaging, not the least of which is cost-efficiency. It only takes one custom box for you to do what four cardboard boxes would have done before. But other benefits include easier storage, reduced labor costs, and less wasted space in your warehouse.
The custom boxes shipping containers are also more environmentally friendly than their cardboard counterparts because they’re reusable. In this blog post; we’ll go through the steps on how to make a custom shipping container that will meet all your business needs.
Table of Contents
How to Make a Custom Shipping Container
1. Get your Measurements
Measure the height and length of the box you need. To make sure it’s safe for transport, every custom container should be at least six inches longer than its contents. If this isn’t possible, you’ll have to choose another type of packaging instead.
Now measure how many layers deep your object will be going into the box— multiply that by two (since each layer doubles in-depth) then add eight inches on top of that measurement to account for space between boxes during shipping.
For example: if you’re packing a five-inch item with four other items around it inside one big box, double their combined heights which is 20″ tall, and also add 16″ on top of that so they can all fit snugly inside.
2. Cut Paperboard to Size
Cut a sheet of paperboard so it’s about two inches larger all around than your height measurement. This will make the custom container box sturdier and more durable, which is especially important if you’re shipping heavy or fragile items inside it.
3. Measure and Cut the Bottom
Measure out your length measurement plus an additional two inches on each side. This will make sure that the box can’t be tipped or spilled easily, which is especially important if you’re shipping liquids inside it. Cut this shape from paperboard as well using a straight edge to guide your knife for uniform sides
4. Add Reinforcing Tape
Place the bottom into one of the long edges, and then use an awl to poke holes along the other three on each side. Now place a strip of reinforcing tape along these four lines and fold it over so that it sticks together.
5. Cut the Top
Measure out your height measurement plus two inches on each side. Cut this shape from paperboard as well, then use a straight edge to guide your knife for uniform sides
Add reinforcing tape in the same way that you did with the bottom so it can be attached and stay securely shut during transport.
Place one of these flaps over onto another long edge (which should already have some custom box pieces glued together) and fold all four edges up. Make sure they’re lined up neatly before taking an awl to poke holes along them once more.
6. Add the Other Side
Now place strips of reinforced tape along these four lines and fold them down so they stick together. Continue adding sides until you’ve closed off the top, bottom, two short sides, and both ends with a piece from each corner in between.
Fold over any excess paperboard on all six outer corners then take your knife or scissors to cut away any extra bits around the seams that will be going against your object during transport.
This way a good custom box can be created for any product packaging and it also makes the custom box to look different from any other kind of packaging that serves a competitive edge to your product.
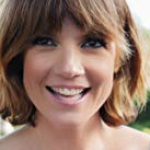