
Injection molding is a method for mass production of plastic parts and is better than other processes, given its capability to economically make complex plastics parts with tight tolerance, however, a suitable injection mold must be designed, and manufactured accordingly.
The injection mold design directly determines the injection molded products quality and molding efficiency. The injection mold is a complex system comprised of multiple components that are subjected to many cycles of stress & temperature.
There are normally trade-offs in injection mould design, with lower-cost molds sometimes resulting in lower molding product quality.
The Injection mold company should strive to make injection molds that are “fit for purpose”, which means that the mould should make plastic parts of acceptable quality with minimal cycle cost while taking a minimum of time, money, and risk.
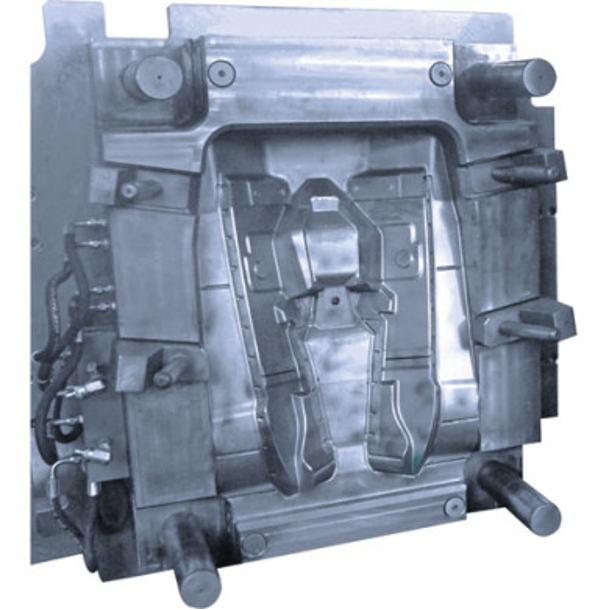
This page is guided to support beginner and expert injection mold companies of both plastic products and injection molds. When you are running your injection molding business, you need to know the overview of the moulding process and various types of injection molds, so that the you can understand the basic operation of injection molds and injection molding process, cost etc.
If you want to buy injection molds or molded parts, find a mold manufacturer China company will be much easy to help you, you do know need to be an expert of injection molds and molding process, the China Mold company will take care the most of the issues for you, but you still need to learn some skill and some ideas about molds and molding process, so that you could have some question in your mind and ask your Chinese mold company to explain you.
Table of Contents
Overview of the Injection Molding Process
Injection molding is sometimes called as a “net shape” manufacturing process, because the plastic molded parts emerge from the injection molding process in their final shape normally no or min post manufacturing processing required to the final parts
The mould is lifted and clamped in the clamping plates in the injection molding machine. The mold typically is connected with the machine platens, there are two halves in the molding machine, the molded parts are formed when the mold closed and the melt material is injected in to the mold cavity, after the mold is opened so that the molded parts can be removed by the ejection systems. Once the part ejection and the mold will be closed to run the next molding cycle. injection molding processes is generally including Plasticization, injection, packing, cooling, and ejection steps.
During the material Plasticization stage, a injection screw within the barrel rotates to convey plastics into melt material by high temperature. The material melt is plasticized from solid granules or pellets through the combined effect of heat conduction from the heated barrel as well as the internal heating caused by molecular deformation as the material is forced along the screw flights. Afterwards, during the injection filling stage, the plasticated melt material is injected into the injection mold by high pressure injection speed of molding machine. The molten plastics go to a mold runner system, through the mold gates, and throughout to mold cavities where it forms the molded product.
After the mold cavity is 95% full filled with the molten resin, the injection packing stage provides some additional resin into the mould cavity as the molten plastics cools and forms.
The plastics material shrinkage changes with the material properties and application requirements, the molding machine basically forces 1 to 9% additional molten material into the mould cavity during the injection packing stage.
After the molten material sops to flow, the cooling system provides additional time for the plastics in the mold cavity to solidify and become more rigid for ejection. After that, the injection molding machine open the moving platen and the attached mold half, then eject the solid molding part out.
Injection molding cycle time
Plastic injection molding cycle include filling time, packing time, cooling time, ejection time, mold open and close time (including pick part up).
The filling time is a small part of the cycle time. The packing time is little more than the filling time, and is often use this packing time to control the plastic molding part weight.
In general, the cooling phase of the injection molding process dominates the whole molding cycle time, there are some of factors that effects to the cooling time,
- Better cooling system design will reduce the mold cooling time,
- Wall thickness will affect to the cooling time, thicker wall requires longer cooling time,
- Material properties requires different cooling time, for example, Nylon requires longer cooling time but PP requires less cooling time.
- Part size effects the molding cooling time, big part requires longer cooling time.
To minimize the molding cycle time and costs, injection mold company needs to design the better cooling systems in the mold, and improve the wall thickness, to make the balance wall on the part design.
Mold opening time and part pick time
Fully automatic production will reduce the part picking time, but the operation of fully automatic molding processes requires better injection mold design, manufacturing, and mold testing. Not only the mold operates without any hang-ups, but also the quality of the plastic molded parts must consistently meet the requirement.
Hot runner feed systems could reduce the cycle time as well, hot runner systems allow the use of less plastic resin while also reducing injection and packing times, and it is runner-less so that can save the raw materials.
Injection Molds and molding processes can be optimized to minimize mold opening, ejection, and mold closing times.
Conclusion
There are many types of the injection molding process (such as gas assist injection molding, insert molding, two shot molding (2k molding), co injection molding, injection compression molding) that are used to support different industry requirement.
These advanced molding process can increase the quality of the injection molded parts, but will increase the complexity and risk of the mold design, mold manufacturing and molding process, and advanced molding process will require the high technology of mold manufacturing and molding process skill, as well as the high cost for mold manufacturing and molding equipment
We are mold manufacturer in China, we offer injection molds & injection molding processing service, post manufacturing, assembly, packing and delivery service to the world companies. If you have any project that need injection molds, you make need to think about us.
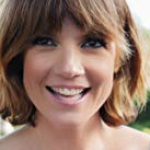