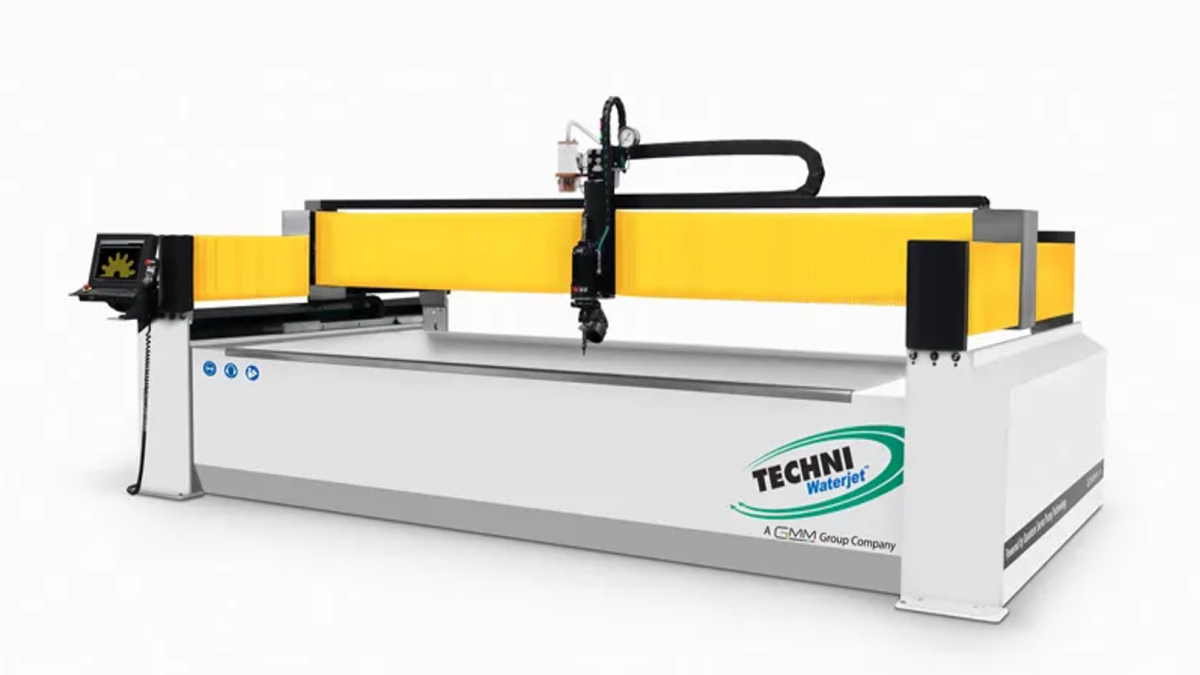
Table of Contents
Benefits for the Industry
Shops are not limited to metal fabrications anymore with waterjet cutting equipment. They can now search for business opportunities in previously unexplored areas.
A waterjet can cut almost any 2-D material. It is usually capable of cutting materials up to 6 to 12 inches in thickness. However, thicker materials can be cut if the operator takes it slow enough. The waterjet’s small-diameter cutting stream–approximately 0.040 in. It can produce precise corners with extremely high tolerances, up to 0.050 inches.
Waterjet is also a “cold cutting” process that does not produce heat-affected areas or burnt edges. This means that most applications require little to no secondary operations. Exotic materials such as titanium, Hastelloy(r), and other alloys are cut easily with no need to predrill holes.
It doesn’t stop there. The waterjet is capable of cutting both hard and non-hard materials such as titanium, stainless steel, and aluminum. It can also cut munitions, exotic alloys, composites, and stone. Soft materials can be cut only with water, while hard materials need to be mixed with fine grains abrasive garnet.
Waterjet cutting machines are a great way to diversify in today’s world, where fabricating shops want to avoid the downs and ups of being too closely tied to one industry segment. These shops can cut glass, stone, or foam materials as easily as they can metals.
Clear Understanding of Cutting Glass
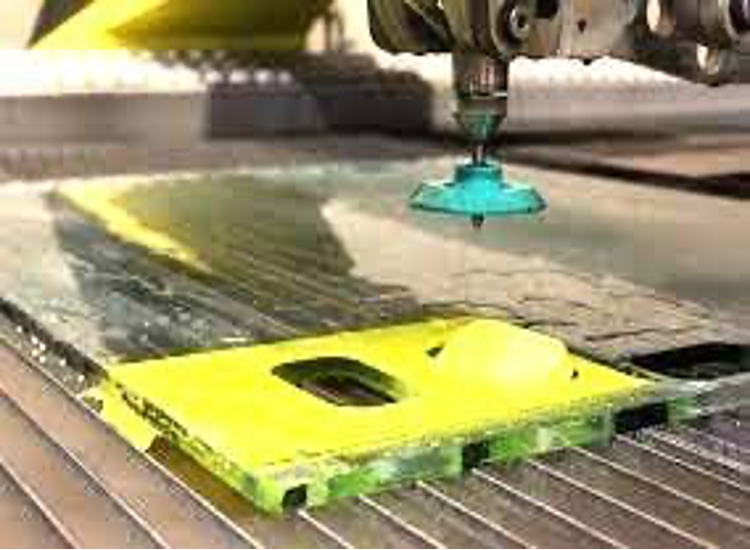
A waterjet is suitable for glass cutting. A fabricator(in the role of a waterjet cutter) can easily go from cutting sheet metal to cutting delicate glass without any setup or tooling changes. A waterjet can actually cut thicker, bullet-resistant, laminated glass, up to 4 inches.
This fine cutting stream allows almost any shape to cut with virtually no force applied to the glass. This is in contrast to traditional glass-cutting methods like a spinning router, where loads are applied to the surface. Waterjet operators must use low pressure piercing to avoid shattering glass.
A waterjet can also be used to cut glass quickly. Waterjets can cut glass up to 0.25 inches thick at speeds of more than 40 inches per minute (IPM).
An operator will use the same abrasive as for cutting metal when cutting glass with a waterjet. It is most likely garnet. The operator uses less abrasive. For cutting metal, one lb. one lb. of abrasive is used for cutting metal; 0.25 lb. for cutting glass. To 0.50 lb. Consumed.
The waterjet leaves only a few thousandths inch of taper, just like metal cutting. Customers don’t have to worry about this because traditional cutting methods typically leave 0.50 inches. The waterjet abrasive leaves no chips, tiny fractures, or faults.
Waterjets with five-axis cutting heads can be used to cut glass that is hard to cut with traditional methods.
What are some examples of uses for shop-cut glass? Waterjet-cut glass is commonly used for cutouts, holes, backsplashes, frameless showers, and mirrors. Fabricators can cut any radius, contour, or profile with a waterjet. The waterjet can make an inner radius of as little as 0.020 inches. It can cut an inside radius as small as 0.020 in.
The Hard Facts of Cutting Stone
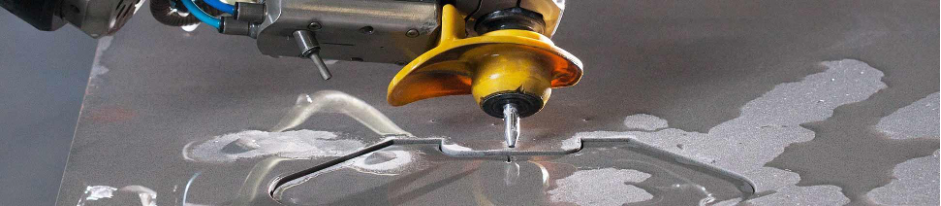
The waterjet’s small stream size makes it ideal for stone cutting. A waterjet stream can handle materials as thick as 6 inches with extremely high pressures (up to 60,000 PSI).
The quality of stone and the speed with which the waterjet cutter can cut it depends on what kind of cut is desired. Black granite, for example, is extremely hard and needs a slower cutting speed. Yellow granite, on the other hand, is denser. A waterjet cutter can cut through granite countertops up to 1.25 inches thick at 5 IPM to 12. IPM, and backsplashes up to 0.75 inches at 8 IPM or 15 IPM.
Garnet is again the best abrasive for cutting stone. The amount of abrasive used to cut stone is approximately the same as that used for cutting metal.
Material handling is perhaps the most important aspect of stone cutting. Stone slabs are heavy and must be handled carefully. Customers will not accept a marred surface.
The slabs are usually five ft. x 6 ft. or 6 ft x 7 ft. in size and must be moved vertically. The slabs will crack or break if they are moved in the horizontal position.
When working with stone materials, shops should think about upgrading their material handling equipment. Although vacuum lifters are possible, slabs still have a high risk of cracking. Material handling systems can be designed to lift the slabs vertically and then move them slowly with hydraulic arms to the horizontal location atop the cutting table. This equipment has a maximum load capacity of 1,100 lbs.
Most stone-cutting applications do not require a waterjet to cut. While polishing is usually required, secondary finishing will not take as long with a waterjet.
The waterjet cuts stones very precisely, and a shop does not need to grind them afterward. The waterjet cutter machine can be programmed to deliver stones in the required dimensions.
What are some examples of uses for shop-cut stone? You can see the obvious uses all-around your house: kitchen and bathroom countertops, backsplashes and flooring, as well as landscaping accessories.
When the Waterjet Hits the Rubber
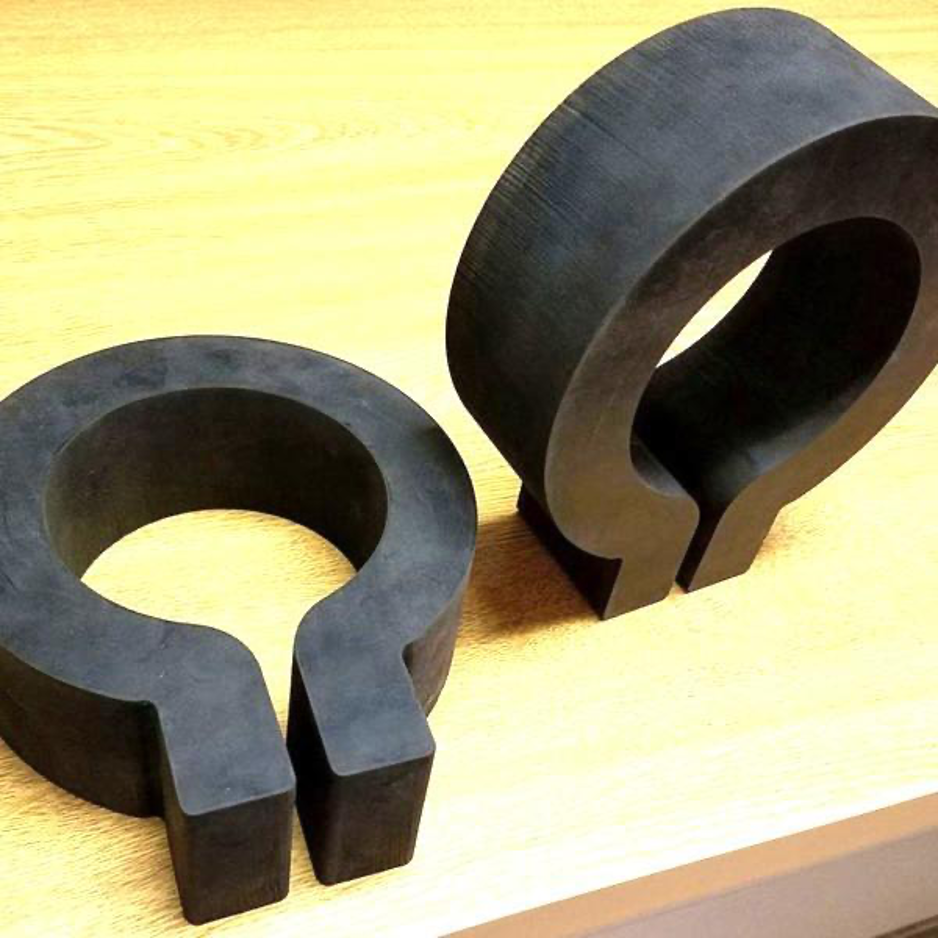
Waterjet cutting is also suitable for foam, rubber, plastic, and insulation. Shops don’t need to worry about handling surface-sensitive materials like glass and stone.
Programmers can create tight nests. The waterjet’s fine cutting stream can also allow for high material yields. A waterjet can do stack cutting up to 8 inches thick and being possible.
Speed is the real advantage of a waterjet for cutting these materials. Multi-cutting heads can be combined with conveyor systems to achieve speeds up to almost 1,000 IPM.
These rubber, foam, and similar materials are typically cut with a steel rule, which must be designed and built for each job. The die can be costly and time-consuming to make, so a waterjet is a better alternative.
Shops that cut plastics need not worry about it interacting with the material or releasing noxious fumes. These interactions are eliminated by the cold nature of waterjet streams.
Nonmetal Cutting in Future
As people become more aware of global trends, the cutting of nonmetals will increase. Glass is increasingly being used in Asia and Europe for architectural elements, as well as residential buildings.
Composite materials are replacing metal in aerospace components. Boeing has, for instance, made it clear that the 787 Dreamliner will largely be made of composite materials.
Fabricators can use a waterjet cutter machine to take advantage of these trends and also cut the metal plate and sheet that were used in the construction of the business.
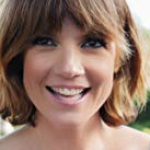