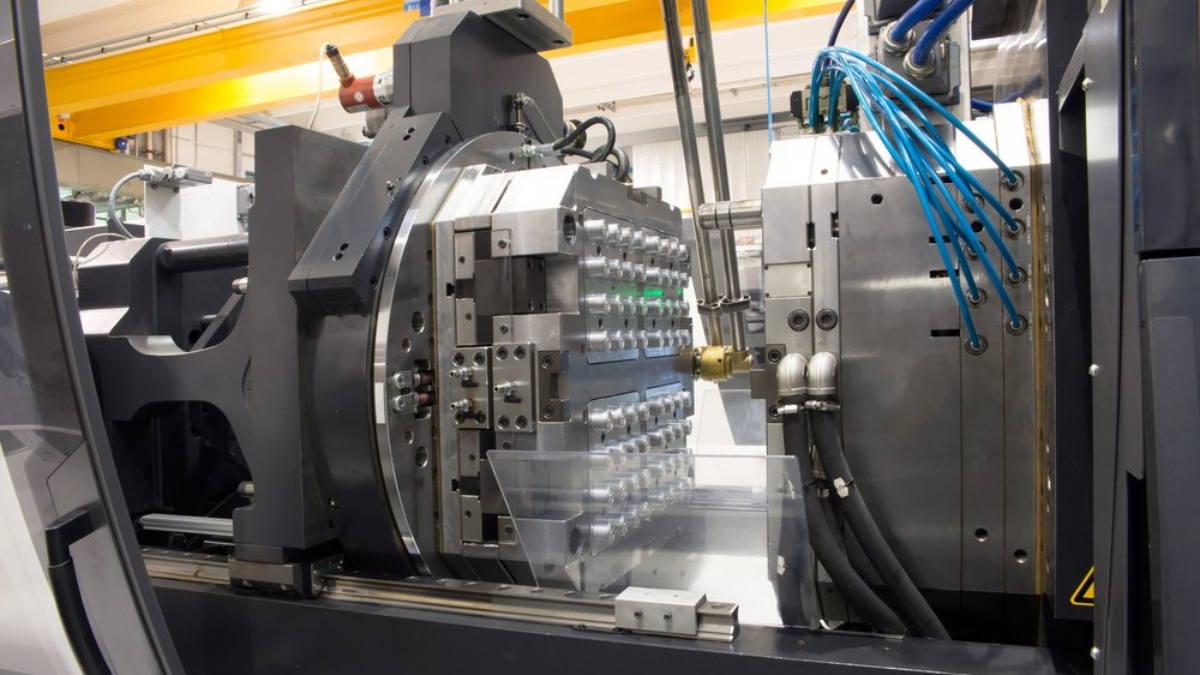
If any brand-new product has some defect visible to the naked eye, such as weld lines, a customer will naturally stray away from it. Moreover, when dealing with plastics, this defect could also cause functional failure to a product. So, without a doubt, weld lines must be avoided. But how?
The secret of avoiding weld lines in precision injection molding is to ensure that the plastic is adequately heated. Also, the cross-sectional area of the nozzles of the molds has to be of proper size.
Considering the weld lines can severely damage the plastic product and lead to the failure of an entire production process, you need a better knowledge of why it occurs. So, let’s talk about that first.
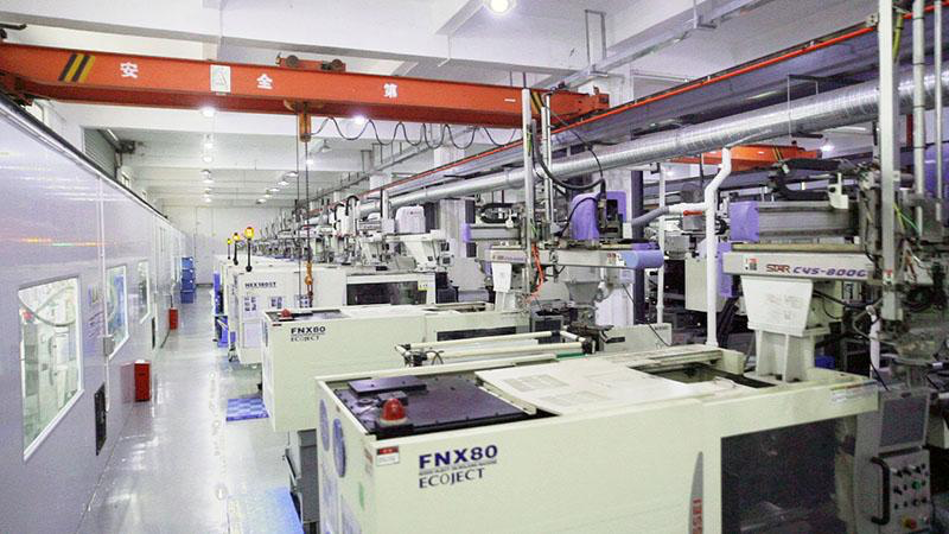
Table of Contents
What Are Weld Lines and Why They Occur?
In precision injection molding, a weld line or knit line appears when two or more streams of melted plastic meet at different temperatures inside the mold. There’s a high chance that the streams won’t mix with each other perfectly. So, weld lines appear because of the not-fully blend in the place where the two flows meet each other.
This can also cause the physical strength of the object to decrease to a certain amount. To better understand how this phenomenon forms, you must know what happens in the precision injection molding when melted plastic flows through the molds.
In this process, the flow forms a natural and smooth flow front. However, when it comes in contact with an obstruction, it splits into different parts and goes around the object. The flow then reconnects in the front, which leaves a slight blemish at the surface. This slight defect is known as the weld line or knit line.
In addition, a meld line will be formed when the fronts of the two flows mix at an unusual or oblique angle. Usually, meld lines have better strength than weld lines.
Causes of Weld Lines
There can be numerous reasons why weld lines occur during injection molding. The mold, material, and even faults in the molding procedure can be a factor in causing weld lines. Here are the common reasons for weld lines.
1. Mold
- Too many injections points. It creates more meeting points in the precision injection molding process.
- Tiny cross-sectional area. It increases the flowing resistance and prolongs the time for the plastic flow to go through the mold.
- Lack of cold material cavity. The correct setting of the cold material cavity will eliminate the weld lines.
- Rapid and uneven cooling. It solidifies the plastic flow too early to blend together.
- Bad exhaust. It leads to the air bladder, which finally becomes a carbonation point.
2. Material
- Incompatible or using too much release agent. In precision injection molding, the release agent is usually only used on the parts that are not easy to release the mold, for example, the screw thread part.
- Poor fluidity. The slow-flowing material may solidify before blending together.
- Too much moisture. Moisture is also a factor that affects the blending at the meeting point.
3. Molding
- Low temperature. The low temperature during the molding process may decrease the merging ability of the plastic flow.
- Low injection pressure. Low injection pressure in the precision injection molding will slow the flowing speed.
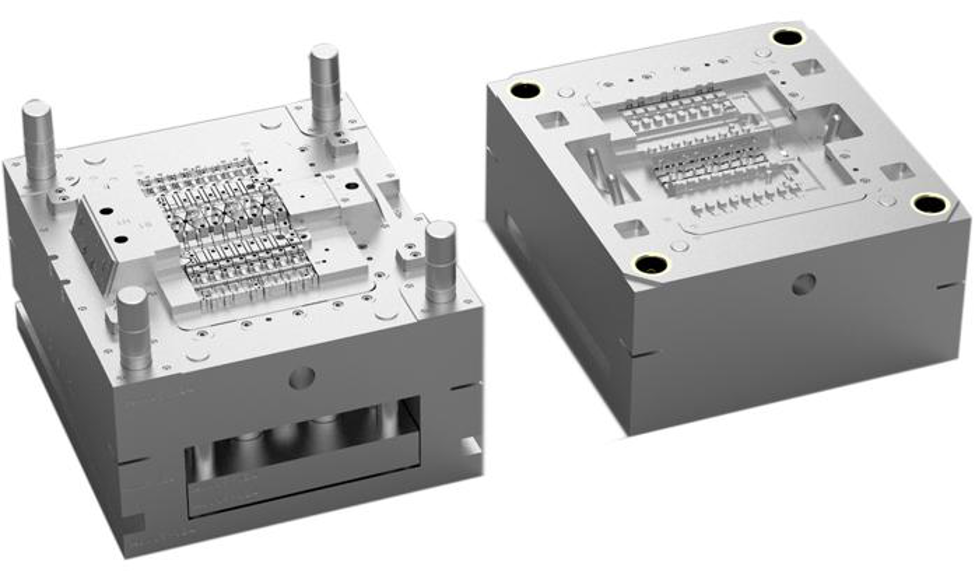
The Solutions to Weld Lines
Weld and meld lines are known to cause structural problems. They’re also visually unacceptable. Therefore, it’s evident that weld lines should be avoided at any cost. If removing a weld line becomes too tricky, it should be manipulated to form in the least sensitive area. Avoid weld lines in the areas that need to be sturdy or look smooth.
Although the problems that cause weld lines in plastic bodies are very intricate, some methods can help resolve or minimize them.
1. Mold
Use larger flow gates but in small numbers
Set a cooler material cavity
Control cooling water flow
Change position of cooling water channel
Add vent holes at the collecting points
2. Material
Select the best release agent that’s suitable with the shape, materials, and molding conditions
Decrease release agent dose
Add lubrication
Pre-heat to dry the raw material
3. Molding
Heat the barrel and nozzle
Increase the injection pressure
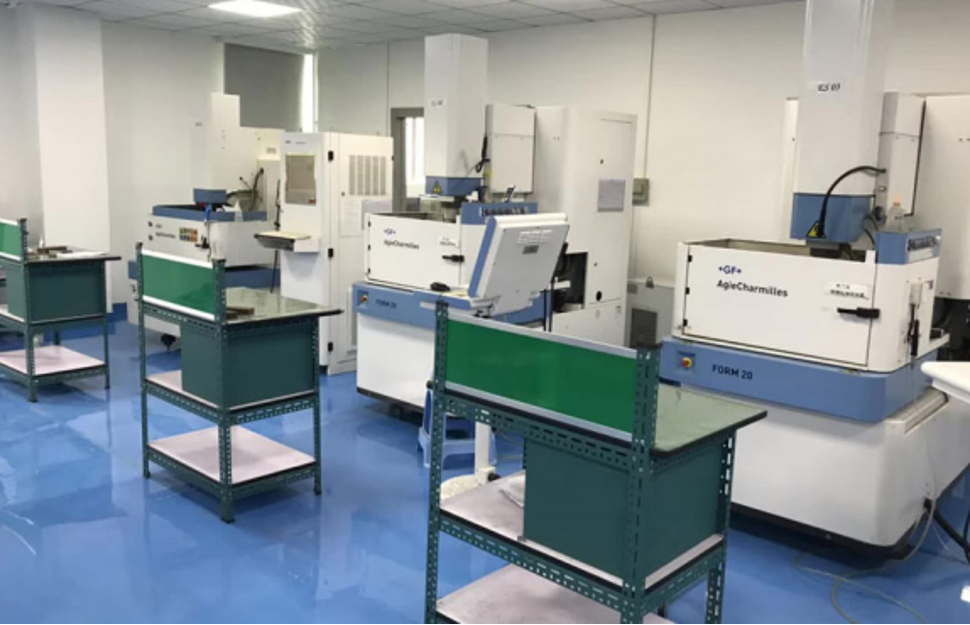
Why Choose Abery?
Abery uses only the latest technologies and state-of-the-art techniques for plastic injection molding. It is ruling the plastic injection molding China market in this domain at this moment, working with hundreds of customers worldwide. And It’s only possible due to its research in the field and capable workforce.
Abery’s precision injection molding techniques ensure every mold is made with the highest precision using automated techniques. Its dedication to the craft endows them with the opportunity to work with many big names such as Honda. The famous brand attracted by Abery’s expertise should be a testament to the quality you can expect from this company.
Conclusion
As you can see, weld lines can be a severe issue in manufacturing plastic products, and its causes can range from inappropriate manufacturing processes to even using poor quality molds. So, keenly follow the proper procedures when manufacturing your products and also order your molds from trusted companies with a rich portfolio like Abery.
If you require precision injection molding for the highest quality, contact them today to begin working on your project, and their high-efficient team will give you the best solution!
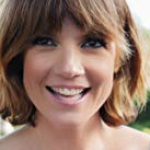