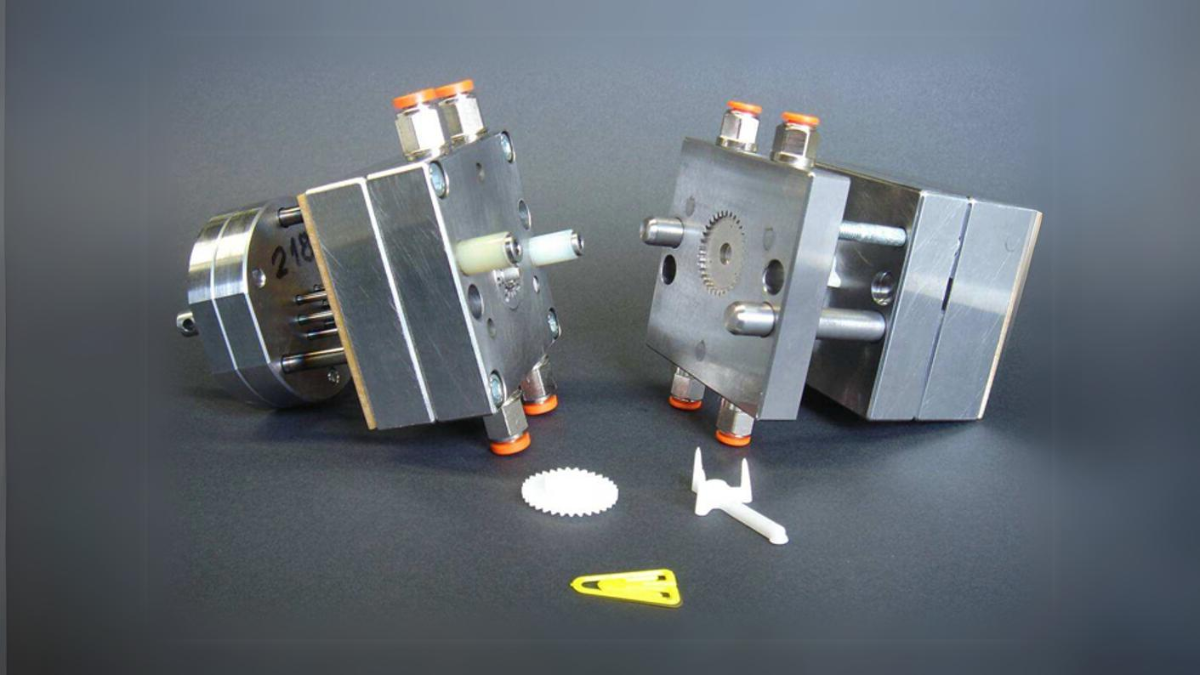
In a fast-evolving tech era, manufacturers encounter numerous challenges but ensuring top-notch parts and products for customers remains paramount. To create quality components, you require tools capable of producing them, which is where rapid tooling occurs. It has transformed the product design and prototyping sector, emphasizing the significance of selecting the right tooling approach. Choosing between soft and hard tool manufacturing hinges on your unique application, budget, and quality criteria.
Table of Contents
The Definition of Hard Tooling and Soft Tooling
Hard Tooling
Hard tooling is one of the rapid tooling types. Hard tooling uses robust materials such as steel or aluminum to craft molds or dies. For instance, aluminum molds can be employed for high-volume injection molding. The procedure commences with a design, which is subsequently converted into a physical mold using machining methods.
Soft Tooling
Soft tooling is another type of rapid tooling; it offers flexibility, using materials such as silicone rubber or polyurethane. It’s well-suited for short production runs and prototypes. The process starts with a master pattern, often created using 3D printing, which is then used to make a mold. Soft tooling materials are adaptable, facilitating more accessible modifications, which is why it’s a top choice for projects with frequent design changes.
Comparing Hard Tooling and Soft Tooling
Here are some detailed comparisons of rapid tooling types, explicitly focusing on hard tooling and soft tooling:
1. Cost
Because of its endurance and material requirements, hard tooling has a higher initial cost. However, it becomes more economical per unit when used in large manufacturing numbers. For soft tooling, the opposite is usually accurate, as it has lower beginning costs but is frequently less cost-effective for large-scale manufacturing.
2. Lead Time
Soft tooling, as rapid tooling, typically has a shorter lead time than hard tooling because it’s more flexible and more accessible to modify. Hard tooling requires more time due to higher quality standards and machining demands.
3. Customization
Soft tooling is more adaptable to design changes. As it is generally used for short production runs, alterations can be made without incurring significant expenses.
4. Complexity
Hard tooling can handle more complex designs due to the strength and precision of the materials used.
5. Tolerance and Precision
Hard tooling offers superior tolerance and precision, so the end products meet exact specifications.
6. Materials and Durability
The materials and durability of the two rapid tooling are different. Hard tooling excels in durability and is ideal for tools used in extensive production cycles and harsh conditions, handling various materials like plastics, metals, and composites. In contrast, soft tooling often works with materials such as silicone, carbon fiber composites, and fiberglass. Still, it has shorter lifespans, especially in large-scale projects, leading to faster wear and tear.
7. Maintenance and Repairs
Hard tooling has a longer lifespan and is less prone to wear and tear, which lowers the cost of maintenance over time. Soft tooling has lower durability, is suitable for specific materials, and has a shorter lifespan.
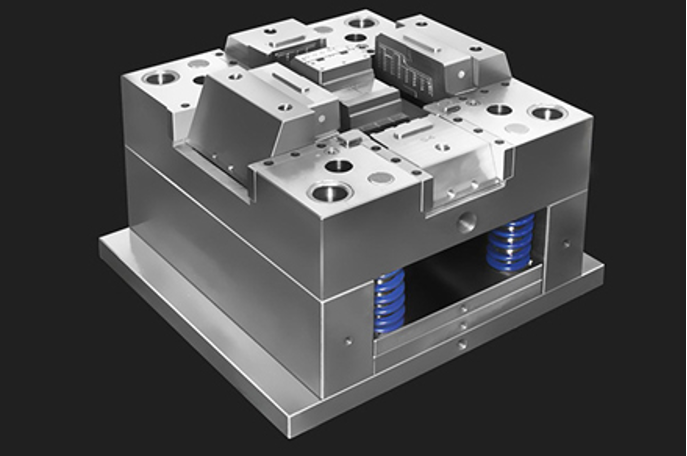
Choosing Between Hard Tooling and Soft Tooling
Choosing between hard and soft tooling is essential, as it impacts production speed, expenses, and final product quality. Hard tooling is ideal for high-precision, large-scale production. In contrast, soft tooling suits prototypes, short runs, and scenarios demanding design flexibility, allowing multiple iterations in early product development. It also offers a cost-effective entry point for budget-conscious industries. You can refer to the above points when selecting rapid tooling.
JOBR’s Rapid Aluminum Tooling Service
JOBR is a top professional injection molding company that supplies high-quality molds to clients in China and overseas. With JOBR Tech, customers can access comprehensive one-stop services, facilitating a seamless transition from design to production. As a rapidly growing injection molding manufacturer, JOBR’s rapid tooling services offer a superb solution for manufacturing industries seeking enhanced productivity and reduced time-to-market, with costs more than 50% lower than those in the U.S. and European markets.
JOBR utilizes a wide range of materials, such as Acetal, Nylon 66, HDPE, PBT, and more, in its rapid processing, ensuring versatility and top-notch production quality. Furthermore, JOBR operates on a 24-hour production cycle and maintains a 100% inspection rate, guaranteeing punctual delivery and exceptional product quality.

Conclusion
Established in 2013, JOBR is a leading player in the rapid tooling industry. They offer various services, from quick prototyping to injection molding and CNC machining. Known for their commitment to high-quality results, operational efficiency, and customer satisfaction, combined with competitive pricing, they are a top choice for your manufacturing needs. Get in touch with them to procure top-notch.
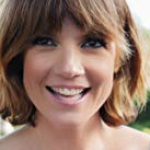