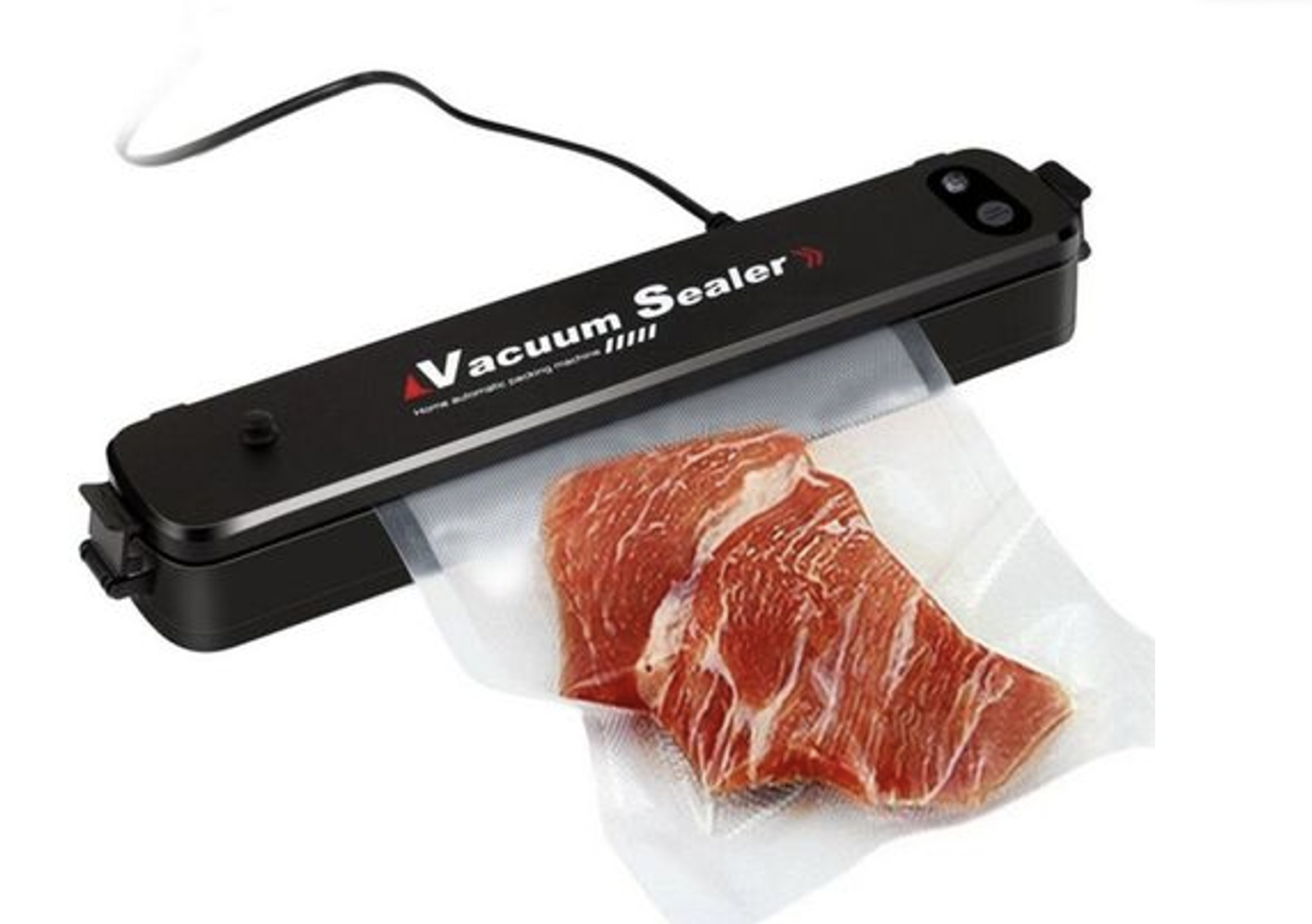
If you have been tempted to buy goods purely based on their looks, you would know the essence of packaging to the success or failure of a product. Still, the ideal packaging makes a product aesthetically pleasing and excellently enhances its functionality and utility. Also, products have better chances to survive the shipping hazards or shelf life at a retail store if properly packed.
One such machine that’s gaining popularity and provides great convenience to sellers is the automatic sealing machine. It can be used easily, guarantees a superior quality finished product, and is extremely simple. The food industry benefits the most from industrial robot manufacturers and automatic sealing machines since food production is now automated and plastic packaging helps conserve many food items and prevents contamination before reaching customers.
Here are the different types of sealers and sealing equipment you should know.
Table of Contents
Band
Band sealers are used to seal pouches, and they can be either vertical or horizontal. Generally, a moving pair of bands grasp the top of the package and move it past heating. Packages can be backed by a movable conveyor or held by the sealing bands. Some models have a tilt feature that permits packages to be sealed tilted upward to avoid spillage.
Clamshell
Clamshell sealers are handheld tools structured to add tamper resistance to the self-locking clamshell. These are typically used for premade salads, sandwiches, hardware items, and more.
L Bar
L Bar sealers are utilized with film to make three sealed edges from doubled-over lengths of components or from the distinct top and bottom web materials. The L bar sealer makes an end and an edge seal with every cycle, creating an “L” shaped seal.
The open side and rear of each succeeding pouch provide a filling opening which is then sealed. This sealer has a cut-off device to separate the packages. Frequently, they are used in conjunction with heat tunnels and shrink film.
Vacuum
Vacuum sealers are used mainly for food and meat packaging owing to the benefit of low oxygen levels for obstructing spoilage. Vacuum sealer equipment often incorporates a chamber for evacuating the package before sealing the top layer or cover into place. They can be manual, automatic, or semi-automatic machines depending on volume requirements.
Case and Carton
Case and carton sealers utilize taping heads to apply adhesive tape to the flaps of the cases and cartons. Then, they use conveyors to pass the cartons beneath the tape applicator heads. For taping bottoms and tops of cases and cartons, side belt machines are sometimes used.
Cap and Bottle
In cap and bottle sealing, the tamper proof lids under capped bottles are normally sealed inductively with aluminum foil through handheld, fully automatic, or semi-automatic machines. Regardless of the bottle decoration ideas of the product, the bottles are passed through the sealer, then placed with a tamper proof closure held cap until it seals.
Applications and Industries
Heat and impulse sealers are applied in several sectors mainly as a manner of providing a secured layer of coatings and as part of count management. Mostly, sealers depend on heat to weld or melt plastic film to itself or to other packaging components, including trays, cardboard, and the likes.
Ambient air sealers are utilized in packaging products that are not affected by oxygen. In contrast, vacuum sealers are used to carry out airless packages for food. In addition, some boxes are made with modified atmospheres (MAP), such as baked goods, nuts, and more.
Selecting the ideal sealer all boils down to package rate requirements. Small hand sealers do well for low-volume applications. On the other hand, fully automated machines serve the needs of the high volume market. Sealers usually work with preformed pouches, clamshells, blisters, and so on.
However, exceptions exist, including the L-bar sealer, which makes its pouch from a single web of packaging film. Moreover, a low volume user of preformed pouches might opt for a jaw sealer, while a higher volume user might select a band sealer.
Considerations
Note that the material type and thickness have significance on the choice of impulse or direct heat sealers. Generally, thicker components benefit from the always-on condition of direct heat seal bars since they require more extended heat penetration to generate basic seals. However, some materials, including foils and coated films, also seal better using direct heat sealers.
Impulse sealers offer advantages in terms of efficiency and safety. Since they simply bring out heat when sealing actively, impulse heaters power their heater bars on demand. The materials fitted to impulse sealing are PET (polyethylene terephthalate), PVC (polyvinyl chloride), polypropylene, and polyethylene.
Seal integrity is crucial, particularly for MAP and vacuum packages. The suitability of materials used for lids, trays, and so on should be checked with the material vendors. Packaging films can be treated with adhesive to impart unique features to the package, like peel ability. Sealers rely on the three variables – time, temperature, and pressure to create good seals.
Conclusion
In a nutshell, sealers and sealing equipment play a big role in different industries, especially in the food industry. Just imagine the high rate of food and other goods’ fast rate spoilage without being sealed correctly and properly.
If you are looking for a reliable seal machine or seal solutions, you better check out https://www.levapack.com.
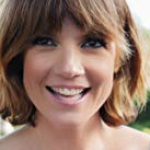