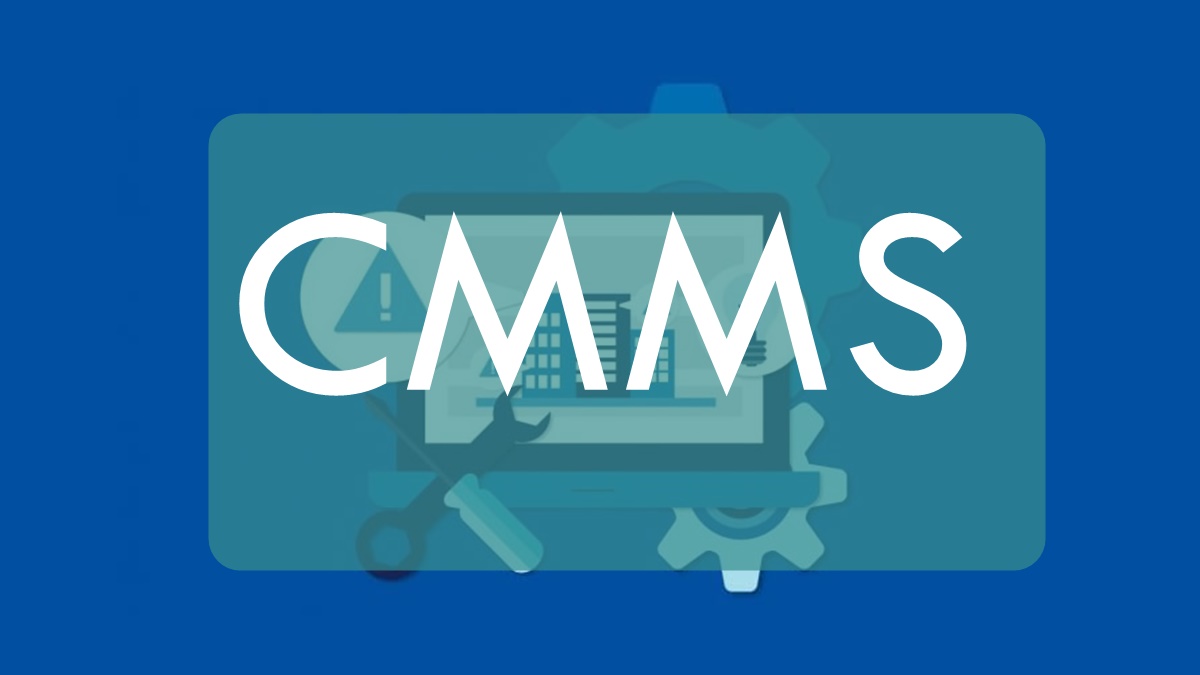
CMMS is a short form of Computerized Maintenance Management Software. It is a program that helps you to track activities related to planning, cleaning and inspecting assets or equipment and machinery.
A good CMMS ensures that the production in a company runs as designed, minimizes down time and increases productivity. So what are the advantages that your organization would enjoy with the implementation of a CMMS?
Table of Contents
Minimizes Downtime
A breakdown of your company’s equipment is expensive. It requires you to immediately put corrective measures in place, which causes the warehouse operations to stand still. It can also damage the company’s reputation as it will miss on delivery timelines.
Implementing a good CMMS helps you to schedule maintenance activities that will reduce the number of breakdowns. A reduced number of breakdowns means a minimized downtime which in turn saves a lot of money.
Helps in Scheduling Predictive Maintenance Tasks
A predictive maintenance best practice identifies defects before they become severe problems thus reducing the number of breakdowns. Planned and predictive maintenance is essential for a company’s productivity. It causes fewer disruptions into the organization’s day to day activities.
One way in which CMMS captures predictive maintenance is through automated work orders. You can create predictive maintenance triggers depending on time, condition and usage in a CMMS. The triggers activate the work order, which you can consequently schedule and assign. The task becomes much more manageable, smooth and leads to a reduced number of breakdowns.
Simplifies Inspections and Makes Repairs Easy
Through a CMMS mobile app, it is easy to see an asset’s diagram, history, location of spare parts, etc., by just logging in to the app. It makes it easy to inspect and repair an asset; therefore, there is downtime reduction to the bare minimum.
Downtime occurs each time an asset needs repairs and inspection. While such incidences can be unavoidable, a CMMS helps you to plan downtime at the appropriate time such as during the closed hours or when the workers are not in the building. It is because downtime inefficiencies can cost you heavily when it happens during the production hours.
Helps You Avoid Rework and Manufacturing Scrapes
Rework and scrape is one thing that costs a company’s hugely when it comes to manufacturing. It is costly in regards to energy, time, waste and lost production. Not to mention that it is tough to make up for that expense without the team working overtime.
Predictive maintenance through a CMMS implementation helps keep your assets healthy and working maximally; therefore, you combat the problem of substandard production. It enables the maintenance team plan, schedule and execute maintenance tasks early enough to avoid interfering with production.
Helps in Tracking and Reporting Maintenance Costs
A CMMS software keeps track of every maintenance activity or completed work orders including labour, spare parts and other expenses. It makes it smooth for you to make a report based on the costs, identify where the budget was spent and make an informed repair or replacement decisions.
The best part is that, if you want to prove the value of maintenance, you can compare the expense of reactive and planned maintenance.
Automated Work Requests
While it is common for maintenance managers to receive work requests via word of mouth, phones, sticky notes, or whiteboard, none of that is suitable. It makes them spend unnecessary time creating work orders and data inputs; time that would otherwise be useful elsewhere.
A CMMS software simplifies all that work by automating the work request process. The employees can set up preventive maintenance triggers, log work requests or connect to sensors that create work orders depending on the real-time condition of that particular asset.
Improved Access to Maintenance Resources
Searching through files manually to find a solution to a breakdown is tedious. Such an inefficiency prolongs downtime and leads to failed audits. A CMMS offers a centralized way of tracking down maintenance resources. You can attach manuals, videos, inventory requirements and any other work order that helps technicians do the work efficiently in less time.
The bottom line
Investing in a CMMS leads to planned maintenance activities that increase the organization’s efficiency and profits.
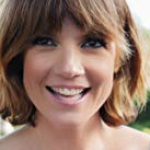