
SOP stands for standard operating procedures. They are more than your typical training how-to. There are many moving parts in your business. To keep your business running smoothly, all of those moving parts must work together. That’s where SOPs come into play!
These are the essentials that keep your business moving. They keep your business running smoothly, and more importantly, they are essential for your success. Who doesn’t want this? When we speak of standard operating procedures, we mean it. Here’s everything you need to know about them.
Table of Contents
What are the SOPs?
Your staff will be able to do their job most efficiently by using Standard Operating Procedures (SOPs). These are written job instructions that describe in detail how to complete a particular procedure or set of tasks correctly.
But what is their purpose? They are to create a consistent and uniform process and an end product.
You know precisely what steps you need to take to reach a particular outcome by using SOPs. SOPs eliminate all doubts, uncertainty, or debate regarding a process. They are a great way to quickly onboard new staff members and make processes uniform.
Types of Standard Operating Procedures.
Checklists
One of the easiest ways to create a standard operating procedure (SOP) document is by using a checklist. A checklist is the easiest to make. Create a heading (the process for which you want to create standard operating procedure guidelines) and then add an ideal checklist items that employees need to follow to complete the task. You can create a checklist online using Bit, or you can print it out and hand it to your employees.
Step-By-Step Guide.
A step-by-step bullet list works similarly to checklists. It describes a procedure in clear, concise steps.
Hierarchical Lists.
You can make hierarchical bullet lists or checklists if your procedures are more complicated and require additional information. You can add hierarchical steps to help you explain complex tasks in one step.
Process Flowchart.
Flowcharts can be a great way to visually show how a process works and provide context for the workflow. A flowchart helps employees understand the process and help them to conceptualize it.
The Benefits.
- Standardizing training programs – Written instructions ensure everyone is on the same page and help you, onboard new employees faster.
- Create a brand identity – Style guides show you how to use colors, logos, typefaces, and fonts in graphic layouts. They also explain how to communicate your brand’s tone in written publications.
- Reduce errors by providing precise and concise guidance on how to prepare for and execute tasks.
- Compliance with the law – precise safety requirements and quality standards help make compliance easier.
- Transparency – Everyone knows who is responsible for what processes and who has the authority to approve each stage.
- Delegating tasks – clear job descriptions allow temporary or permanent substitutes to learn the expectations with minimal assistance from the person who is about to retire or has fallen ill.
Step by Step Guide to The SOPs.
Step 1: Prioritize your SOPs.
There is a good chance that you won’t be able to update hundreds, if not thousands, of SOPs simultaneously. It’s essential to prioritize your tasks.
Step 2: Create your SOPs.
After you have established priorities, it is time to create the actual SOPs. You can start by creating an SOP design team that includes all the necessary members. This team would typically include operators, maintenance technicians, as well as process engineers. If you don’t know the TWI principles, these can give you a solid foundation upon which to create clear and concise training instructions.
Step 3 – Promote and publish your SOPs.
Your staff must be familiar with the SOPs that you have created. You can make them as easy to use as possible by using well-designed portals and dashboards. In meetings, emphasize their importance and discuss the “how” and “why” behind the SOPs.
Step 4 – Train and test your staff.
Next, you need to assess whether your staff actually uses and follows the SOPs consistently. Your staff may not be following your SOPs just because they have completed a training course.
Step 5: Implement & Maintain your SOPs.
Training your staff on SOPs is only the beginning. You’ll need to find out if the SOPs have been used effectively. You should make them a part of your daily organizational routine. Ask staff members regularly during shopfloor rounds if they understand the SOPs.
Do you use the SOPs daily or occasionally? Are staff able to deviate from the SOPs now and again? Is this the case? What is their reasoning? Do they have problems with particular parts of the SOPs? Are they able to offer suggestions? …
What is an Ideal SOP document?
These structural elements are common in standard operating procedures (SOPs):
- Title Page: Kickoff your SOP with the title of the procedure, the unique SOP identification number, date of creation or revision, the employees/team department/ the SOP applies to, and lastly, the name and signatures of those involved in creating the SOP document.
- Table of Contents: The next step is the table of contents. A table of contents summarizes the document’s structure and allows the reader to jump between relevant sections quickly. These are especially useful if the document has a large size.
- Purpose: Describe your goals and objectives for creating the document and how they will benefit you and your organization.
- Scope: The scope of the project describes the boundaries of the document. It clearly explains what the document is all about and what it does. It also helps the reader to understand the SOP’s boundaries.
- Glossary: You can include abbreviations or acronyms that you have used in your document but may not be familiar to the audience.
- Roles and Responsibilities. Identify the key stakeholders (employees and managers) that must follow this SOP. Also, identify what responsibilities they would need to fulfill. This will avoid confusion and hold everyone responsible for their actions.
- Procedures: This section will make up the bulk of the SOP document. It will provide step-by-step instructions on how to complete tasks and any additional information.
- Similar Documents: Add a list of training materials or guides that are related to your SOP.
- Safety and health warnings: A separate section should be added to your SOP explaining what your employees must avoid and how they can perform safe operations. This will not only protect your employees from possible dangers but also prevents you from liability.
- Revision History: To ensure that your readers are aware of the most current SOP, add a revision history.
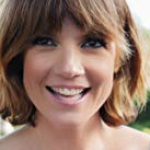