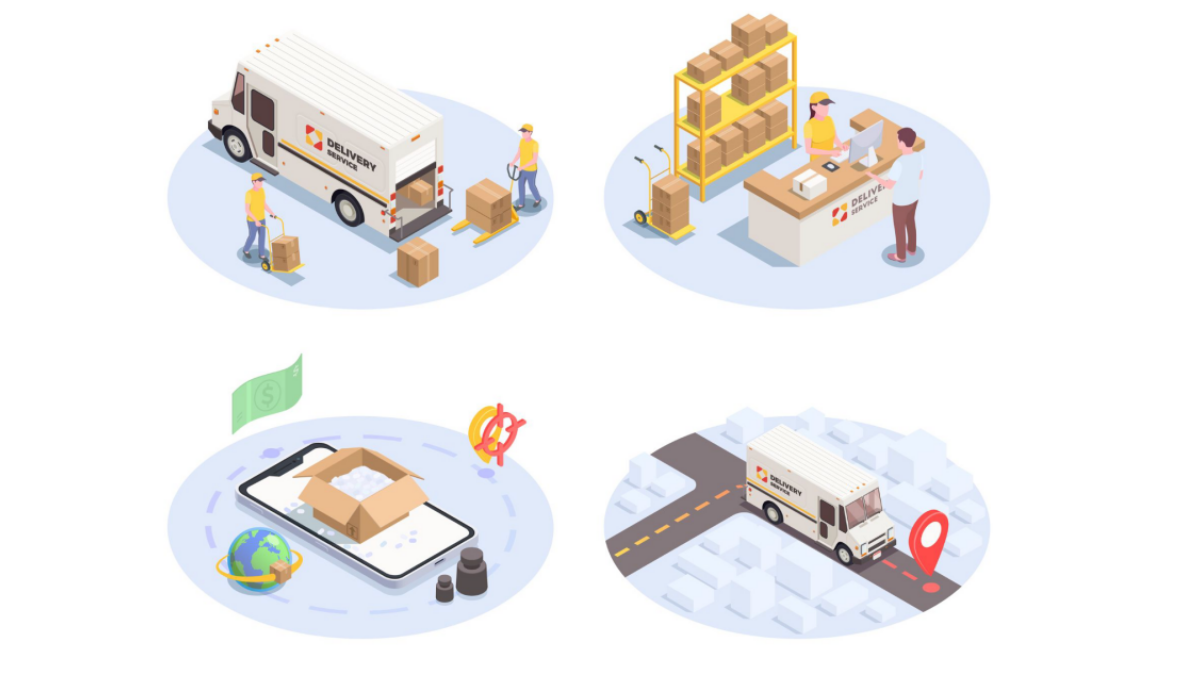
Gaps in fulfillment efficiency can hinder your business’s growth, whether a startup or a renowned brand and reduce your earnings. With sixty-three percent of customers claiming that three days delivery is the standard in today’s consumer-driven economic environment, retailers must devote a lot of time and effort to ensuring that fulfillment operates efficiently. E-commerce businesses must always look for methods to enhance operations, cut costs, and enhance consumer experiences to remain competitive as Amazon continues to dominate the market and rivals struggle to catch up. Your customer satisfaction may suffer due to ineffective fulfillment procedures, including erroneous inventory, which might cost you a lot of money annually. An order fulfillment service takes the task of processing orders away from your business so you can focus on other operations. Following are a few methods you may use to improve the fulfillment process to make it more affordable and successful.
Table of Contents
Prioritize Inventory Accuracy
You won’t be able to fulfill your customers’ orders if your inventory measurements are inaccurate. Consumers anticipate seeing real-time availability and stock levels when placing orders; if this expectation is not met, problems like stock outs may result. The worst-case situation is that clients buy their goods from another supplier, which is not good news for your business.
Setting up good inventory labeling procedures, conducting spot checking, and carrying out cycle counting are some strategies to improve inventory accuracy. You can also employ an inventory management system to remove manual data entry and reduce the possibility of human mistakes.
Predictable Process of Order Fulfillment
Inefficiencies always occur when your order fulfillment procedure changes significantly. If you are unaware of what to anticipate each day in your order fulfillment processes, you could overstock or understock your products and incur higher expenses. Invest in effective order management software to monitor, automate, and predict your systems and increase predictability. Automation has taken on a significant role in logistics and warehousing, and this trend will continue. You’ll save time and get better results through automation. It’s simpler to redirect your focus and put more effort into other areas when your program monitors you.
Improve Order Picking
One of the essential elements of a distribution facility is order picking. It is imperative to optimize the picking process since even minor issues harm your revenue. You can use various techniques, including zone, wave, and small batch picking. Efficiency can be significantly increased by making minor adjustments, such as grouping orders into single units.
Optimize Slotting
Maximizing your slotting effort can result in more successful fulfillment with minor, affordable improvements. Your order fulfillment can be improved with minor changes. To guarantee that your products are sent as quickly as possible, it is essential to treat slotting as a vital function in your fulfillment operations and adhere to best practices.
Order fulfillment companies are on the rise due to the popularity and success of online shopping. However, not all fulfillment companies can do the job efficiently, especially if they don’t employ the above strategies. If your fulfillment company is not reaching its full potential, try employing the above tips to increase efficiency and productivity.
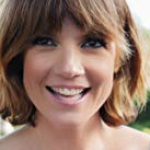