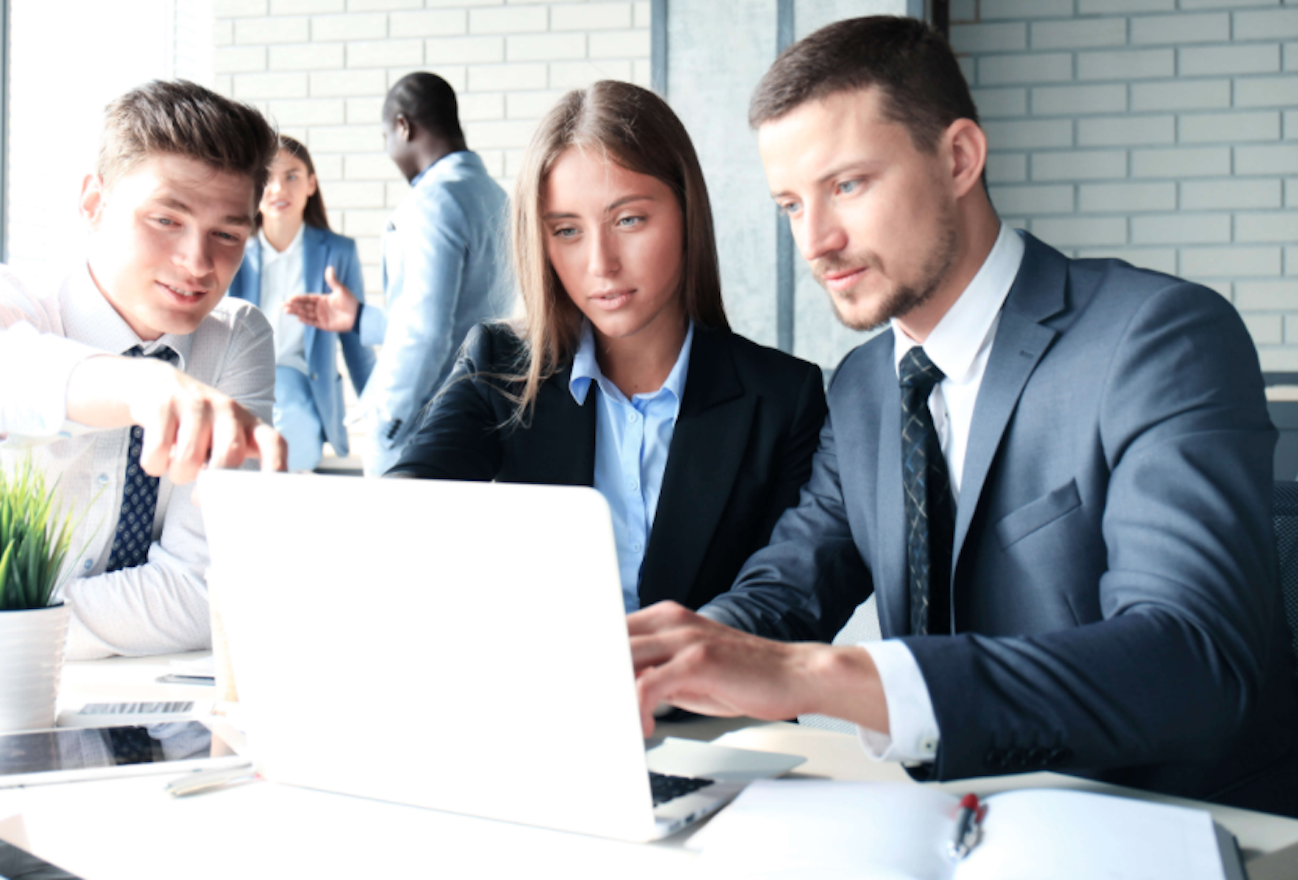
If you have already read about Kanban, you must be aware that it is all about maximizing your customers’ delivery of value by enhancing the output’s speed and quality. This practice is continued until the system reaches the optimal level. Many different types of businesses are already using the Kanban system to improve the value being delivered to the customers, and most of them have been very successful with their effort.
Let’s begin exploring the fruitful Kanban system through these five easy steps.
Table of Contents
1. Visualize your workflow
You will need to begin this process by firstly mapping the process in use. And this visual representation will need to be done on a visual control board. This board can be both physical and digital as well. Every column in the board will represent a particular step for adding value to unit work. It is essential here for you to match every step right from conception to delivery. You will also have the option of having queue columns in between steps as these will represent waiting states.
2. Apply WIP constraints
You should know that you should always apply the WIP constraints by allowing a limited number of work units to be in any particular type of column at a given time. Another important thing that you should know here is that the right number will depend on the context. If you are just starting out, then the best approach would be to set a WIP limit on your most active stage and its number should correspond with the number of individuals on your team. You shouldn’t move work to the next stage (where active work is being done) unless it has enough capacity to handle it.
3. Make policies explicit
This will be the right time to start assigning different service classes to different types of work items. Some of the most common classes that you can use in this case are Expedite, Standard, and Fixed Date. You should also look to make your process as understandable as possible for your team members so they know what is expected of them in each step
4. Measure and Manage Flow
You must remember that we optimize for efficiency, not necessarily speed. This is one of the main reasons why the metrics that we will use here will be cycle time. If you are looking forward to calculating cycle time, you will need to find out the average time taken by a unit of work to move through the system.
5. Optimize using the scientific method
Come out with a hypothesis to determine how the board’s change will affect the outcome and what results you will get. You will need to make the change and then allow your team to use the board in the same configuration for a specific period. Now, you will need to find out whether the difference in the panel is improving the performance. If there are no improvements, you need to decide to either keep your existing board structure, revert back to the old or experiment with another, completely new design. You should know that firms of any size can use the Kanban system, but they should continuously experiment to see what works best for the context they are in.
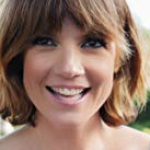